Optimising Equipment Lifespan in Harsh Environmental Conditions
- Reitech Team
- Feb 20
- 3 min read
In industries such as mining, construction, and civil operations, heavy equipment is subject to extreme environmental conditions, including excessive heat, humidity, dust, and corrosive elements. The longevity and efficiency of machinery in these conditions depend largely on proactive preventative maintenance strategies. This article explores some essential best practices for optimising equipment lifespan subject to unfavourable conditions.
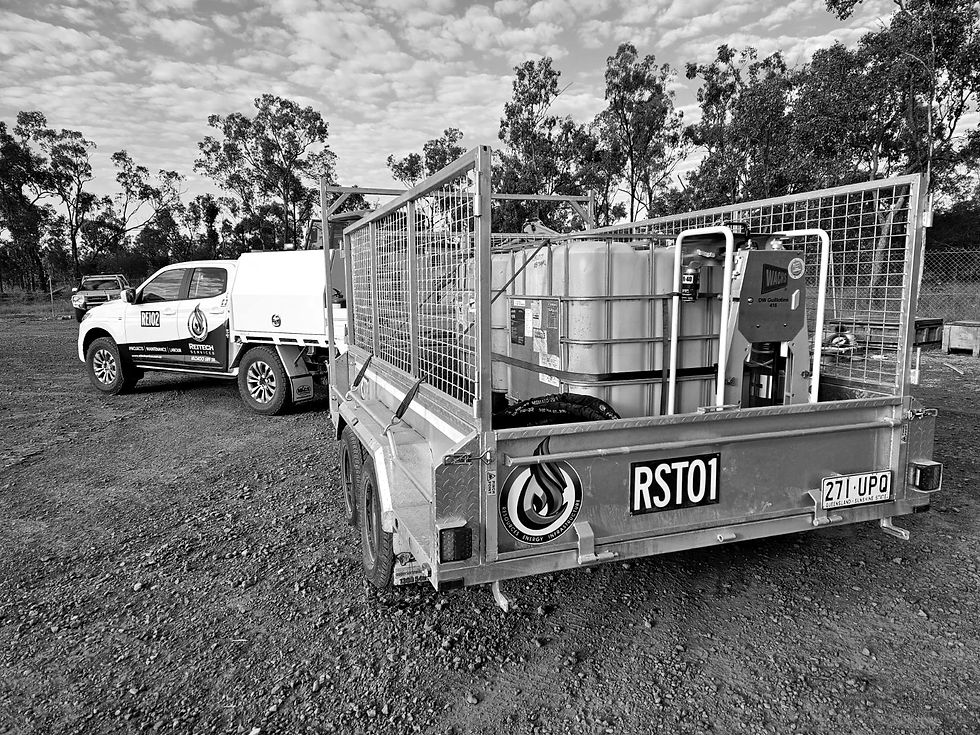
Understanding the Challenges of Harsh Environments
Operating in harsh conditions accelerates wear and tear on machinery, increasing the risk of unexpected failures and costly downtime. The primary environmental factors that affect equipment lifespan include:
● Extreme temperatures: Heat can lead to overheating, oil degradation, and component expansion, while cold temperatures can cause metal contraction and brittleness.
● Dust and debris: Fine dust particles infiltrate machinery, leading to clogging, increased friction, and premature wear on moving parts.
● Moisture and corrosion: High humidity especially in QLD environments, heavy rainfall, and if you are closer to the waterfronts - coastal salt exposure contributes to rust, electrical failures, and structural deterioration.
● Heavy loads and impact stress: Machinery operating under high loads in rugged terrain experiences significant mechanical stress, leading to component fatigue.
Key Strategies for Prolonging Equipment Lifespan
A structured maintenance schedule ensures that minor issues are addressed before they become major problems. We have listed some best practices below:
● Regular inspections: Conduct routine visual and diagnostic checks to detect early signs of wear or damage. These should include detailed reports and photographic records to track deterioration over time.
● Lubrication schedules: Proper lubrication reduces friction and prevents premature component failure. Using the correct recommended lubricants and adhering to strict application schedules can significantly improve machinery efficiency.
● Filter and fluid management: Frequent replacement of air, fuel, and oil filters helps maintain optimal engine performance and prevents contamination. Contaminants in fluids can cause significant internal damage, making scheduled fluid analysis an essential part of maintenance routines.
● Component servicing and replacement: Critical components, such as belts, hoses, and bearings, should be inspected and replaced according to service life guidelines, rather than waiting for failures to occur.
● Storage and protection measures: When machinery is not in use, it should be stored in covered or climate-controlled environments where and if possible.
● Establishing a dedicated maintenance team: Having a skilled maintenance team that understands the specific requirements of the equipment and operating environment can lead to quicker issue resolution and improved reliability.
Case Studies in Australian Industries
Case Study 1: Mining Equipment Longevity in the Pilbara
A major mining company operating in the Pilbara region implemented a predictive maintenance system for their fleet of haul trucks. By using real-time sensor data, they reduced unexpected failures by 30% and extended engine life by an average of 12 months. The investment in proactive maintenance resulted in significant cost savings and reduced downtime. (reference)
Case Study 2: Construction Equipment Protection in Coastal Queensland
A civil construction firm operating in a coastal environment faced ongoing corrosion issues due to exposure to salt-laden air. They introduced a combination of corrosion-resistant coatings, improved drainage around equipment storage areas, and a strict wash-down routine for machinery exposed to salt air. These measures increased the operational life of their machinery by up to five years. (Reference)
Case Study 3: Agricultural Machinery Maintenance in the Outback
Farmers in remote areas of Australia struggle with dust infiltration in equipment. By implementing additional air filtration systems, enclosed engine compartments, and routine compressed-air cleanouts, machinery downtime can be significantly reduced and repair costs decreased substantially. (Reference)
To Wrap Up
Optimising equipment lifespan in harsh environments requires a proactive preventative maintenance approach. Australian industries can minimise equipment failures, reduce costs, and enhance overall operational efficiency by implementing structured inspection routines, effective lubrication practices, strict filter and fluid management, timely component replacement, and protective storage measures. Investing in these strategies not only extends the life of machinery but also ensures safety and productivity in challenging working conditions.
Comentarios